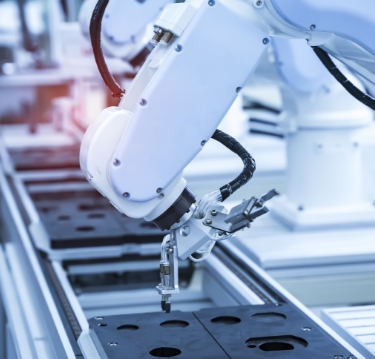
Supporting pneumatic equipment for maintaining clean environments and
automation from the viewpoint of material and seal
designWe provide comprehensive technical support for sealing components used in a wide range
of applications, from robots that
support automation to medical devices that require precision operation.
We
provide optimal solutions for various requirements, such as functional testing on actual equipment,
proposals for
optimal shapes based on FEM analysis, realization of high dimensional accuracy required for
pneumatic equipment, and
proposals for optimal materials for the intended use.
Solutions
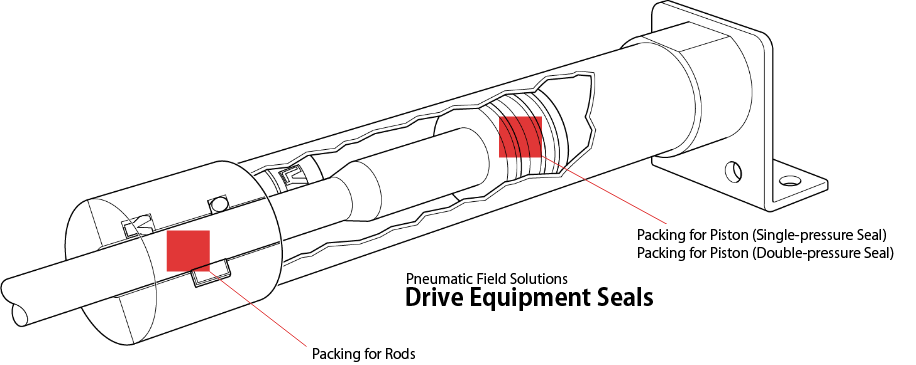
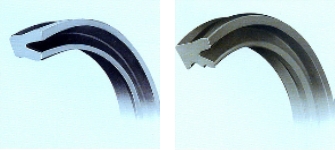
Packing for Rods
Name | Cross-sectional profile | Characteristics | Groove | Size (Rod diameter) |
---|---|---|---|---|
Size(Rod diameter) Y Packingfor Rods (DYR) |
![]() |
|
JIS B2406 P Size |
ø3 to ø20 |
U-packingfor Rods (DLR) | ![]() |
|
JFPS2003 | ø16 to ø60 |
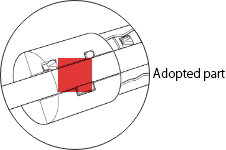
- Material:
- Nitrile rubber 1186-80
- Temperature:
- -20 to 80°C
- Pressure:
- 0 to 1 MPa
- Fluid:
- Air, industrial hydraulic oil, turbine oil, gear oil
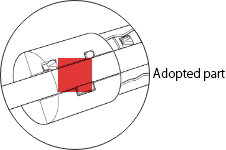
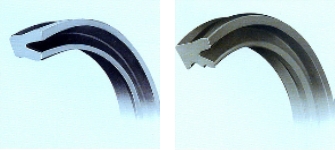
Packing for Pistons
(Single-pressure Seal)
Name | Cross-sectional profile | Characteristics | Groove | Size (Cylinder diameter) |
---|---|---|---|---|
Y-packingfor Piston (DYP) | ![]() |
|
JIS B 2406P Size | ø4 to ø30 |
Y-packingfor Piston(DYP-B) | ![]() |
|
JIS B 2406P Size | ø4 to ø30 |
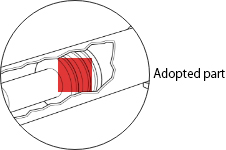
- Material:
- Nitrile rubber 1154-70
- Temperature:
- -30 to 80°C
- Pressure:
- 0 to 1 MPa
- Fluid:
- Air, industrial hydraulic oil, turbine oil, gear oil
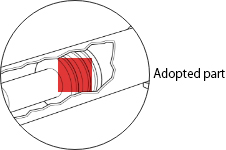
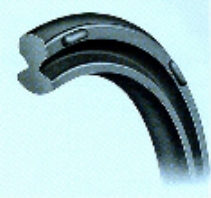
Packing for Piston
(Double-pressure Seal)
Name | Cross-sectional profile | Characteristics | Groove | Size(Cylinder diameter) |
---|---|---|---|---|
Piston Compact Packing (CO-P) for Single System | ![]() |
|
JFPS2004B Series | ø6 to ø125 |
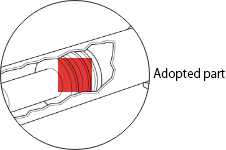
- Material:
- Nitrile rubber 11G6-80
- Temperature:
- -20 to 80°C
- Pressure:
- 0 to 1 MPa
- Fluid:
- Air, industrial hydraulic oil, turbine oil, gear oil
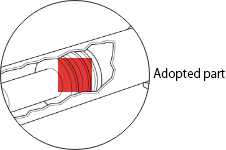
Case Study
Wear
Phenomenon
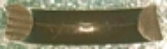
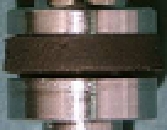
Linear wear scratches parallel to the direction of motion occur on the contact surface.
Cause
The surface roughness of the mating surface is too poor or too
smooth.
Lack of lubrication.
Rubber softens under high
temperature.
Countermeasures
Ensure proper surface finishing. Select appropriate rubber materials. Prevent the entry of contaminants.
Excessive Crushing
Phenomenon
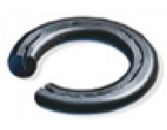
Cracking occurs starting from the inside of the cross-section.
Cause
The amount of internal deformation due to crushing exceeds the allowable elongation of the rubber material.
Countermeasures
Reduce crush rate (typically 5-35%)
Protrusion
Phenomenon
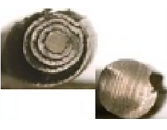
The pressure causes the rubber to protrude into the gap.
Cause
Gaps are large.
Low rubber-protrusion resistance.
Countermeasures
Reduce the size of gaps.
Raise the protrusion resistance.
Use
in conjunction with a
backup ring.
Poor Fitting
Phenomenon
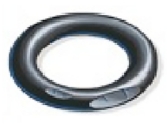
Part of the seal is cut out. Part of the seal is constricted out of the groove.
Cause
Sharp corners, screws or inadequate chamfers on mating surfaces.Seals
are undersized relative to the rod.
Seal too big relative to piston.
The size of the seal does not match
the flange groove.
Countermeasures
Ensure adequate chamfering and eliminate sharp edges. Match the seal size to the groove.
Compression Set
Phenomenon
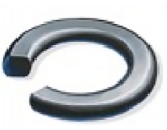
The compressed area becomes flat.
Cause
Operating temperature is too high.
Use of materials with poor
compression set.
It is under-vulcanized.
Countermeasures
Cooling of the sealing area.
Select a material with good
compression set characteristics.
(We recommend the use of our
products)
Twisting
Phenomenon
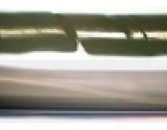
Cracks spiral on the circumference.
Cause
It has a small cross-section for its diameter and a small modulus.
Lubrication is uneven.
Shaft
misalignment.
Countermeasures
Increase the cross-sectional area.
Increase the
modulus.
Improve lubrication.
Reduce eccentricity.
Blistering
Phenomenon
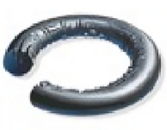
Large and small fissures form on the surface. A portion is also bulging.
Cause
When high-pressure gas enters the rubber and expands (when pressure is released), it breaks the rubber.
Countermeasures
Allow plenty of time when lowering the pressure.
Use hard rubber or rubber with high
modulus.
Use rubber with high gas
permeability.
Make blister resistant
compounds.
Outgas Plasticizer Extraction
Phenomenon
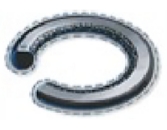
Volume is reduced.
Dimensions are reduced.
Rubber
becomes hard.
Cause
Plasticizer in rubber is extracted by fluid (chemical, solvent, grease, etc.).
Countermeasures
Make rubber materials with less plasticizer or less extractable plasticizer. Remove plasticizer in advance with heat treatment.
Swelling
Phenomenon
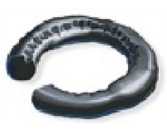
This is a phenomenon in which rubber swells by absorbing
water, chemicals, or other solutions.
When the solution is
absorbed, the rubber is plasticized and its strength is
reduced. Excessive swelling leads to cracking.
Cause
Poor compatibility between the rubber and the fluid used.
Countermeasures
Select appropriate materials for the fluid used.
Thermal Hardening Oxidation
Phenomenon

The rubber hardens.
It hardens
from the surface and progresses with time to the interior of
the cross section. Deformation.
Cause
Temperature is too high.
Deterioration (oxidation) of rubber
materials.
Countermeasures
Select heat-resistant materials with good high-temperature
properties.
Reduce the operating
temperature.
Apply grease to prevent
the surface from being exposed to oxygen.
Ozone Cracking
Phenomenon
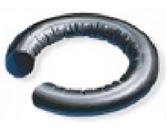
Numerous small cracks form perpendicular to the direction of applied stress.
Cause
The polymer main chain of rubber has an unsaturated structure (double bond). (Ozone reacts with the double bond to break the main chain)
Countermeasures
(FKM, EPDM, HNBR, etc.) Reduce contact time with ozone. Protect the surface.